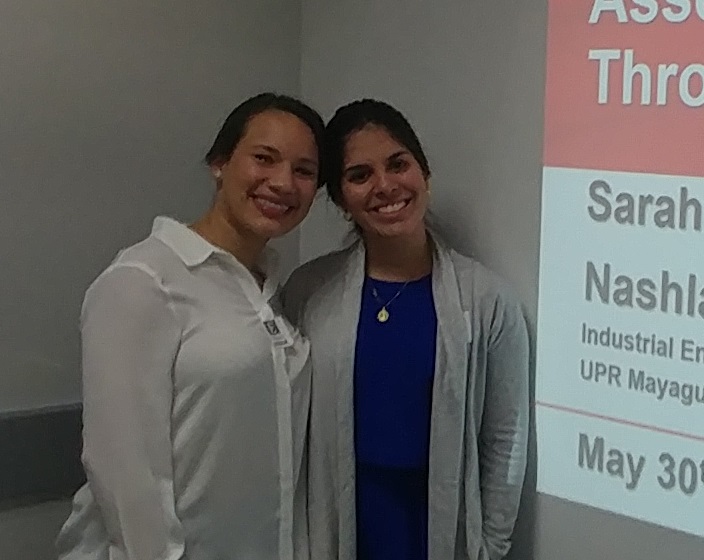
Betzabé Rodríguez, PhD
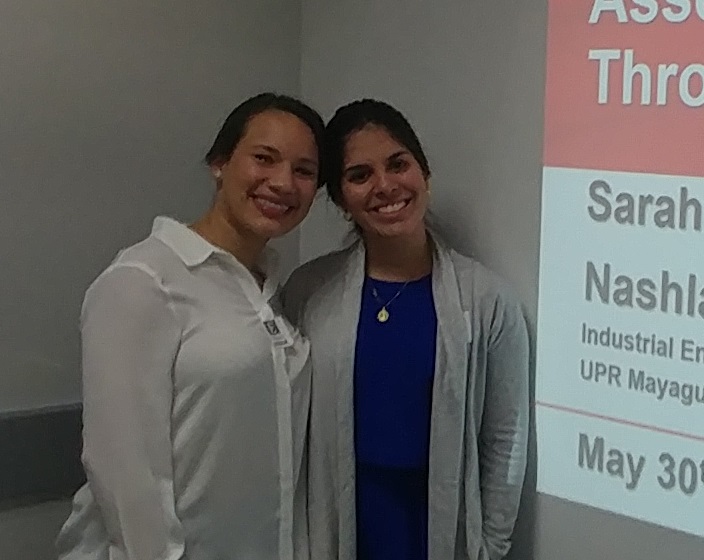
Abstract:
The following study describes the work of senior Industrial Engineering (IE) students who conducted an IE Capstone Design Project in a medical device manufacturing company. An evaluation was conducted to understand why an assembly line didn’t meet their throughput consistently. The aim of this study was to mitigate or reduce the factors that are causing the inconsistencies in the line’s throughput. Therefore, the objectives were to minimize the variability in the process and the accumulation of inventory by at least 5%. As a result, various studies were held such as: work sampling, direct time studies, surveys and a simulation. All data collected led to conclude there was an alarming amount of idle time, an unbalanced assembly line and lean manufacturing wasn’t being applied. In order to attack these consequences, balancing the line was crucial to produce 3 alternatives. Each alternative was simulated to illustrate the impact the line would undergo and remarkably alternative 3 demonstrated the best outcome. Furthermore, a cost analysis also helped to distinguish this final recommendation with a promising potential to improve productivity in the assembly line.
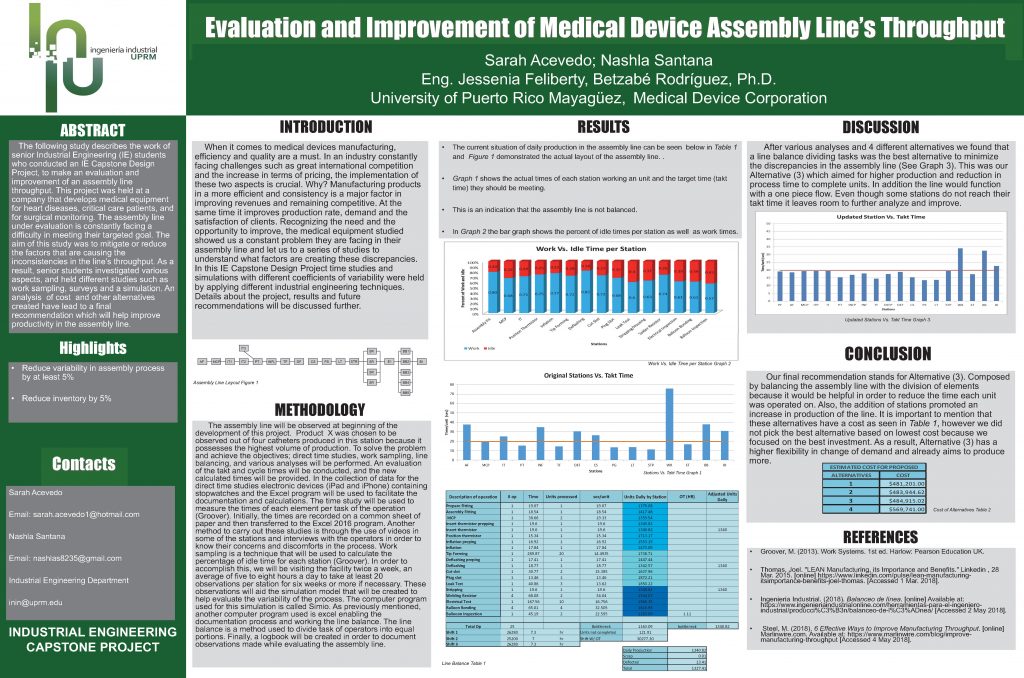