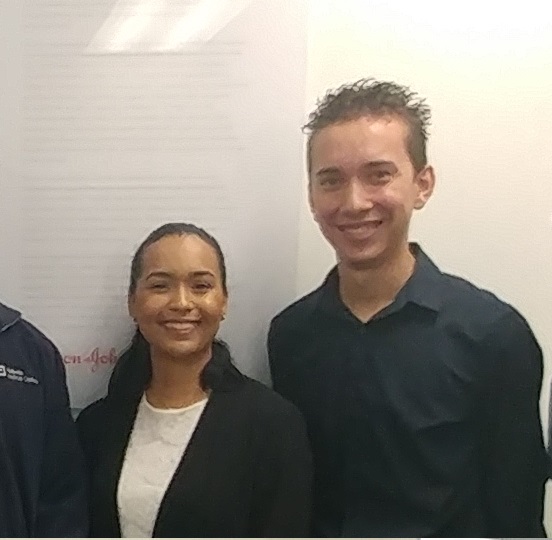
Betzabé Rodríguez, PhD
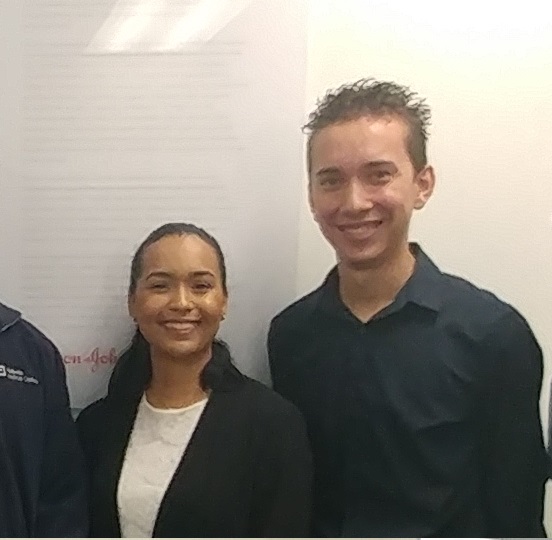
Abstract:
Prior to the implementation of this project, the company was under the impression that a continuous flow work method was the best option to achieve an increase in production output. Hence, this project selected for evaluation purposes the First Pack area of a surgical vision device. Companies and organizations are always improving operation methods in order to provide a product, or service of the highest quality in the most effective and efficient possible manner. To be able to achieve such task, it is imperative to identify areas of opportunity. This packaging area had priority towards continuous improvement. To accomplish such goal, data was collected and analyzed through a time study procedure in order to evaluate current processes to a continuous flow method.At the same time, the current layout of the packaging area was used as a reference point to compare new layout alternatives, which will minimize the workers travelling distance during the completion of their tasks. The results obtained from the completion of these two tasks were two fold: to develop preliminary work designs based on the best work method; and a layout that provides a better work scenario. In this project, a batch processing work method maximized production output by 4.54% when compared to a continuous flow operation by reducing idle time and distances between workstations.

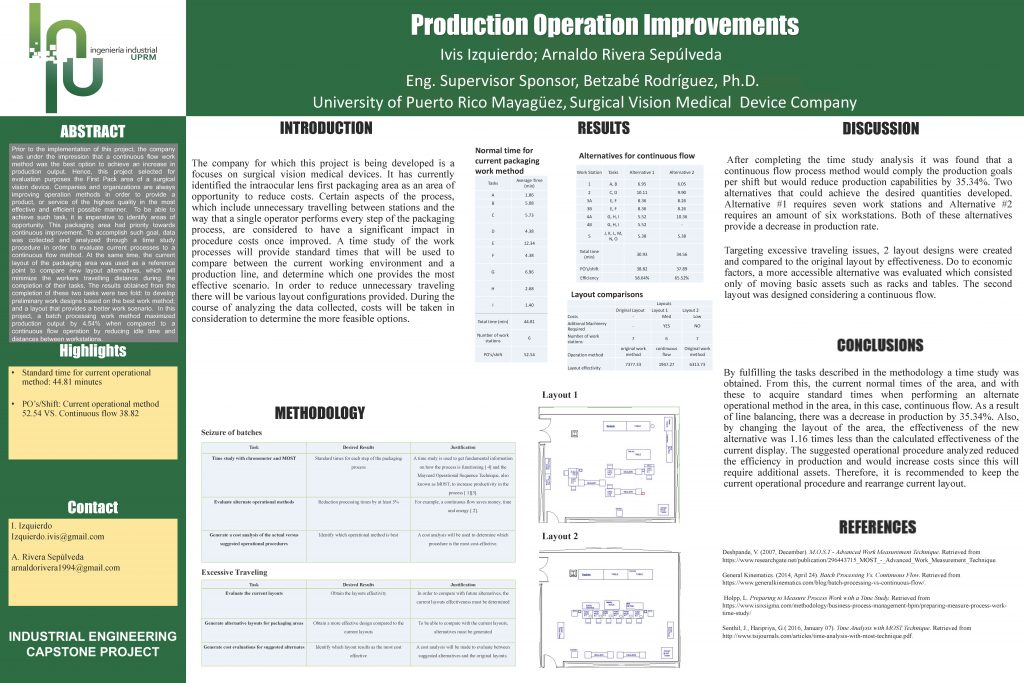